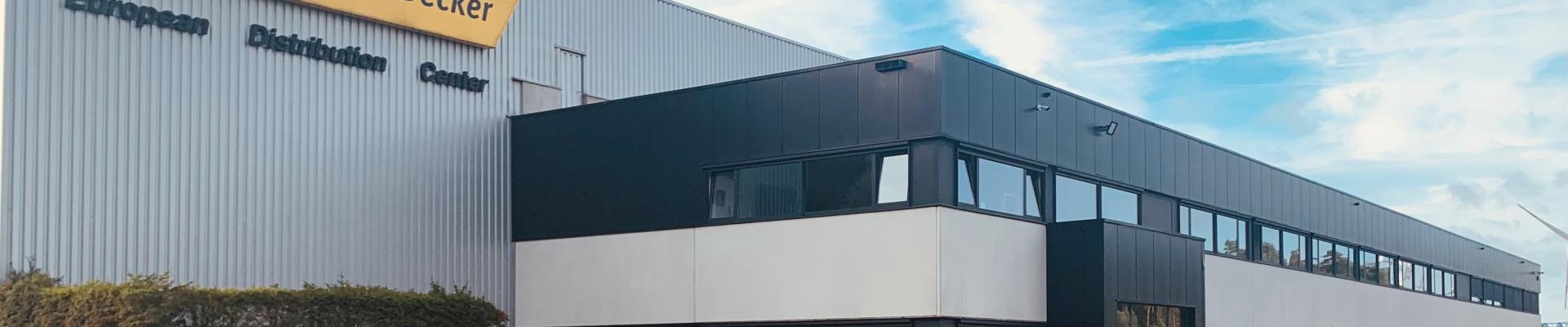
Stanley Black & Decker is committed to ensuring efficient data sharing for the sector as a whole
Stanley Black & Decker has been using the GS1 datapool for a number of years now to share product information with their customers. Currently they already do so for over 5,800 products. By late 2024, the goal is to automatically share all 8,000 products via GS1 GDSN. The company’s e-commerce content specialist Michiel De Buck explains how Stanley Black & Decker manages the way they share their product information.
About Stanley Black & Decker
Stanley Black & Decker is an American company that designs and manufactures electrical equipment and accessories. The company delivers technological solutions for the construction and home renovation sectors and for industrial and professional purposes. To serve the various markets, they run some fifteen different brands. The company aspires to become a world leader in tools by developing innovative products with a focus on sustainability, quality and customer satisfaction. Concentrating on these three aspects exemplifies the company’s bid to provide solutions that meet their customers’ needs in a constantly changing world.
Our interviewee
Michiel De Buck is the central key officer for Stanley Black & Decker’s product information in the Benelux. In this role, he is responsible for maintaining and updating the product information in the datapools as well as for communications with the product managers. In addition, he makes sure all customers have access to the product information.
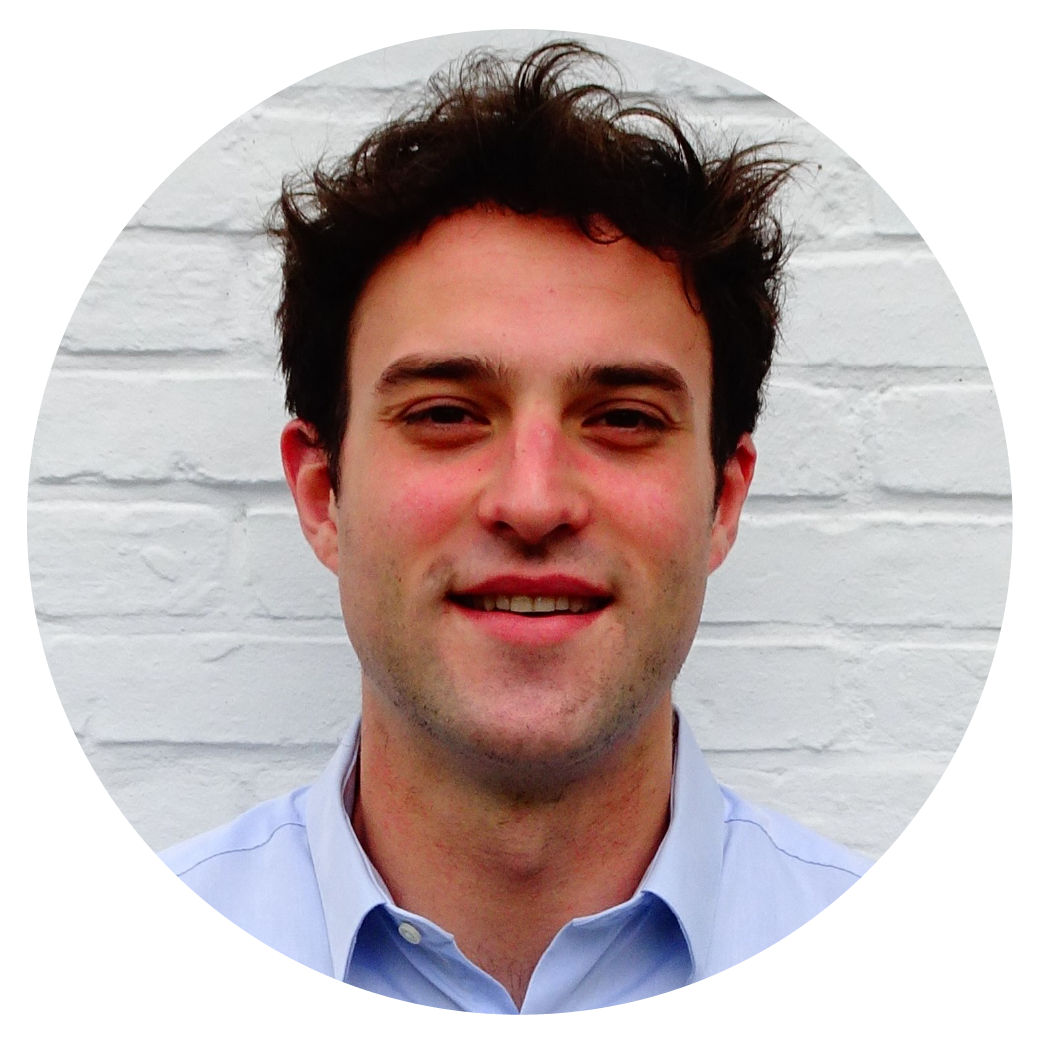
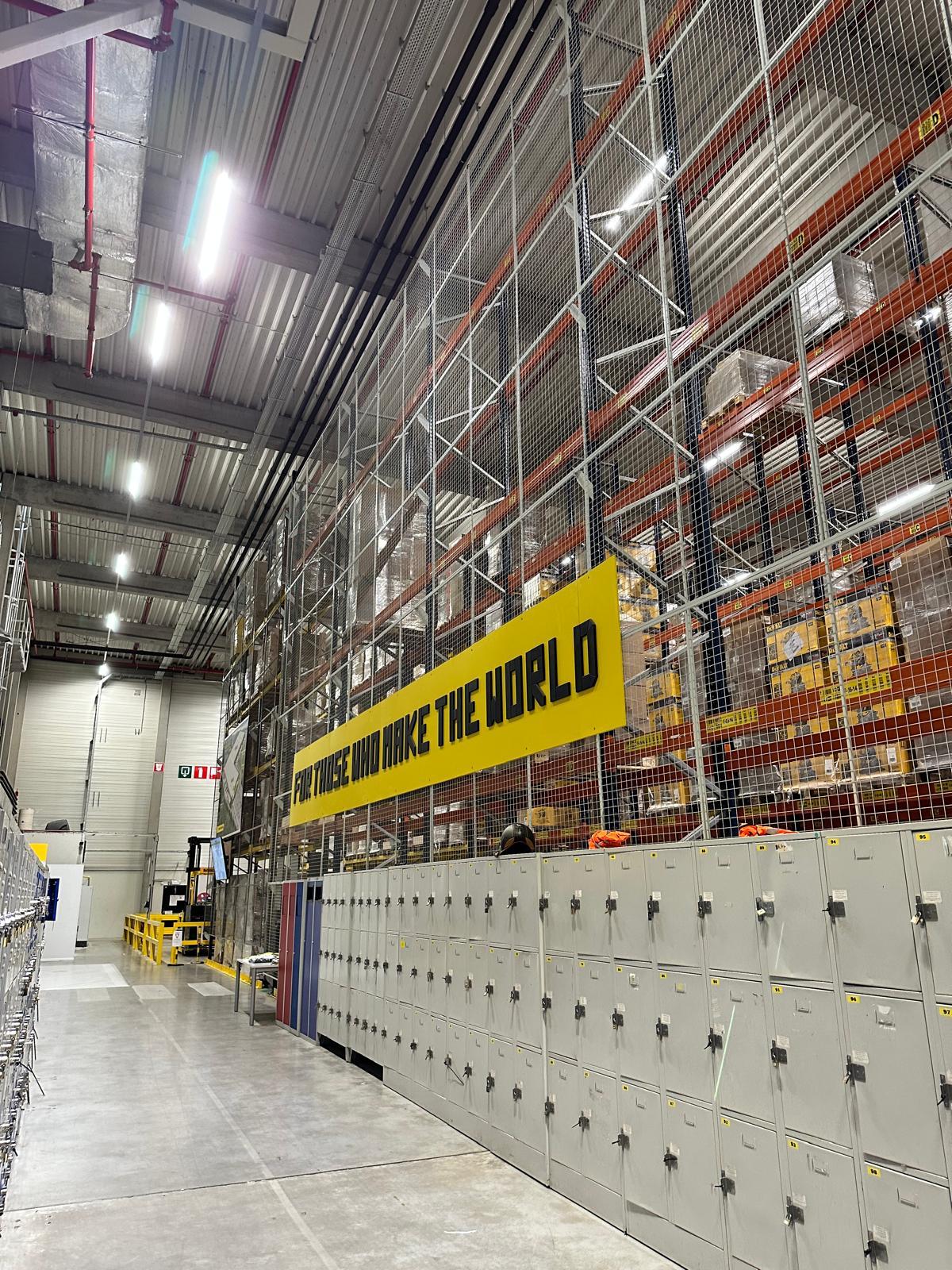
Different datapools
Stanley Black & Decker run a comprehensive product range serving both the professional and the DIY sector. “In order to comply with the GS1 standards for the consumer market as well as the ETIM standards for the professional target market, we decided on a seamless integration of these two datapools by way of a PIM system. Something we set up in tandem with our solution provider SRC”, Michiel goes on to explain.
Data quality up to the mark
“Up until a few years ago, we were somewhat less disciplined in the way we kept track of how which the product information was entered, with a lot of data simply missing”, Michiel says, “which resulted in a rising number of complaints from retailers.” This is when we rolled out the new PIM system so as to centralize data, while taking a closer look at all products per category. “I’m still very pleased with the work the product managers’ team put in”, Michiel comments.
We are currently working hard to make sure the product images comply with the GS1 standards. Nowadays, retailers download the product images from a separate secure platform. Moving forward we are also planning to share these images via the GS1 datapool. “This only makes the exchange of information more efficient”, Michiel adds.
So as to keep the data quality up to the mark and further enhance the quality, we have weekly meetings with all product managers. These meetings monitor the status of the products via a dashboard. “When there is a new data model release, we extensively use the simulation report of My Product Manager”, Michiel says. The simulation report provides an easy to understand overview of products for which action is needed. In addition Michiel receives the feedback from retailers in case data are missing or appear to be inaccurate.
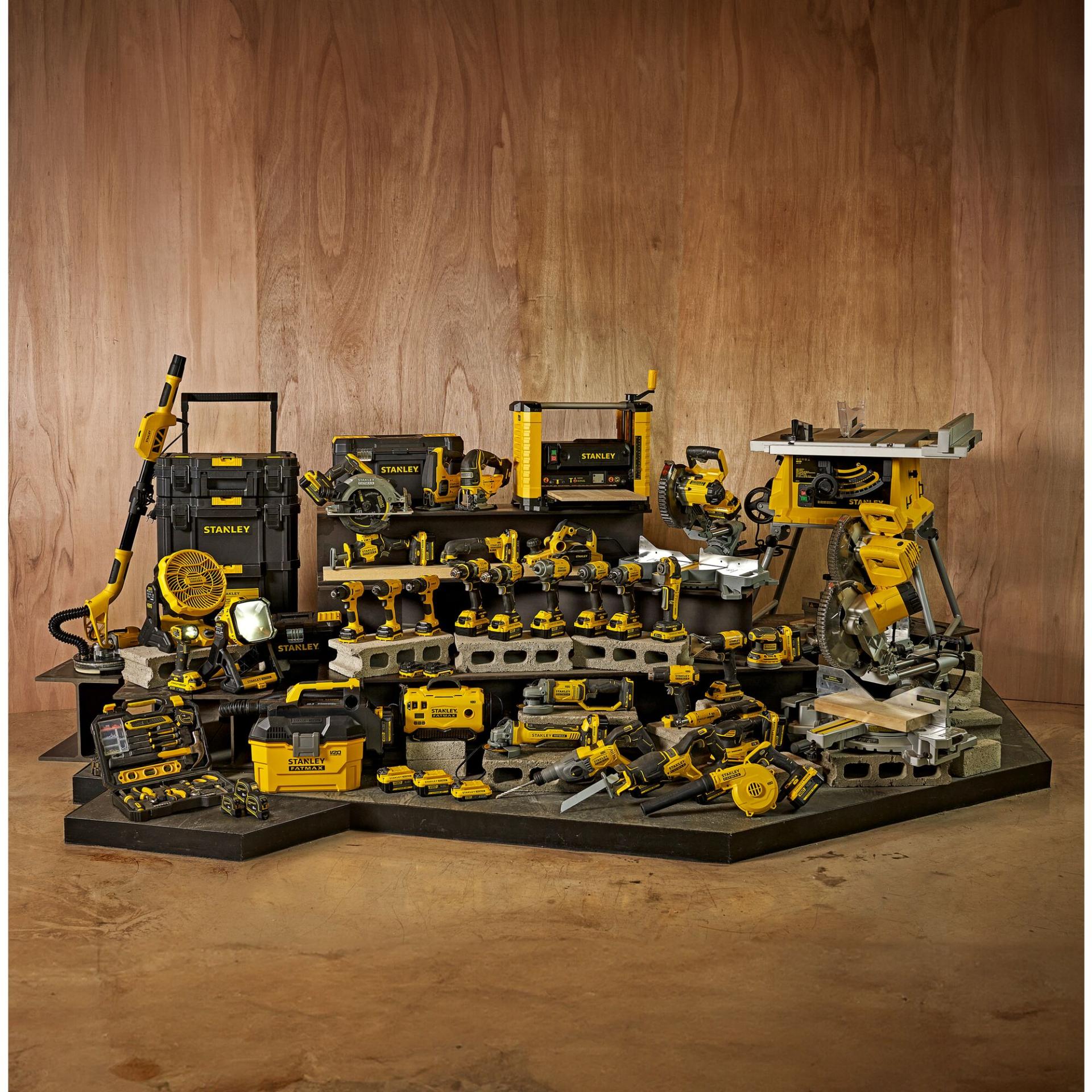
Efficient data sharing
Michael believes that “the GS1 datapool should really be the norm.” Automating product information means all stakeholders have the latest data at all times. Imagine an Excel sheet contains one minor mistake. In that case, the file needs to be resent to all retailers, which they then need to process and incorporate in their own systems. With the GS1 datapool, all it takes is the press of a single button and everybody involved gets the right information without requiring much further work. In a nutshell, the more retailers and suppliers link up to the datapool, the more efficient things go.
Using a data model as a supplier has nothing but benefits. “Thanks to the data model, we know what is important to a customer to make a purchase decision”, Michiel finds.
“We have already sent in a couple of change requests”, Michiel adds. If there are things that are not 100% accurate or are not running the way they should, we can flag up the matter with a change request. GS1 always listens and resolves things asap. Michiel says he would encourage all partners to enter change requests as and when needed to ensure the data model is brought into step with everybody’s needs and requirements with even greater efficiency.